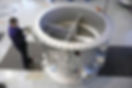
DEBRIS FILTERS
PURPOSE
The BEAUDREY “W” debris filter is installed at the inlet of a condenser to arrest all debris that may obstruct or interfere with the cooling water flow in the condenser tubes and with the eventual downstream tube-cleaning system.
The debris are those that have by-passed the intake screens or grown past them in the pump pits and culverts (seaweed, grass, shells, eels, etc). Debris generated by cooling towers are also to be removed (pieces of packing, etc).
DESCRIPTION
The water enters the cylindrical, flanged spool piece with a rotating screening wheel divided into a number of deep, radial, debris-collection compartments. The downstream face of the compartments is fitted with the patented low head-loss NOCLING™ screening panel which is also fish-friendly, jellyfish and fiber-proof.
The water flows across the NOCLING™ element and the debris are arrested and stored in the compartments. When dirty (head-loss or timer actuation), the wheel starts rotating. It is driven by a peripheral gear and pinion device.
Each compartment passes in front of an upstream scoop which is connected via the flushing valve and pipe to the downstream side of the condenser.
The condenser head-loss provides the hydraulic head to create the backwash flow. All the debris are removed and sent to the condenser outfall.

ADVANTAGES
Keeps the condenser totally debris-free and avoids tube-sheet cleaning
Increases the plant’s power output by up to 1.5%
Pay-back time is generally less than two years
Avoids turbulence-generated tube decay and perforation
Very low head-loss
Improves the efficiency of condenser tube ball-cleaning systems
Virtually no maintenance
Fully accessible from the condenser water box
Can handle any type of debris in large quantities
Backed by over 80 years of experience and over a thousand references.
NECESSARY ANCILLARIES
Differential pressure sensor
Power-actuated flush valve
Electrical control cabinet
Back-wash flushing pipe
OPTIONAL FEATURES
Inspection manholes
Debris concentrator / collector
Ball-injection branches
Support saddle
Seismic qualification
SIZES AND DATA
Standard sizes from DN300 (12”) to DN3200 (128”) (see table)
Larger machines and special shell dimensions upon requestHead-loss about 1.5 V²/2g in most cases for a 6x6 mm mesh aperture (where “V” is the inlet velocity into the spool piece)
Minimum condenser head-loss required for cleaning: 3 m H2O (10 ft)
Available mesh sizes: 2, 3, 4, 5, 6, 10 mm (0.08, 0.12, 0.16, 0.20, 0.25, 0.40 inches)
MATERIALS
-
Shell
For fresh-water applications: painted carbon steel
For seawater applications: lined carbon steel, duplex or super-duplex stainless steel
-
Moving parts and internal fixtures
For fresh-water applications: AISI 304L stainless steel
For seawater application: AISI 316L stainless steel, duplex or super-duplex stainless steel
-
NOCLING (TM) panel
For fresh-water applications: AISI 304L or AISI 316L stainless steel
For seawater application: AISI 316L stainless steel, duplex or super-duplex stainless steel
-
Valve lining
In all cases: EPDM
-
Valve obturator
For fresh-water applications: AISI 304L stainless steel
For seawater application: Duplex stainless steel
-
Pressure-sensing pipes
For all applications: synthetic or stainless steel
LAYOUTS

ELBOW LAYOUT
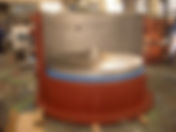
MADE TO MEASURE
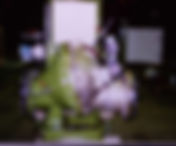
SPHERICAL FILTERS

STANDARD INLINE FILTERS
